Fuel oils are used as fuel in boiler houses and on ships, have a low price and emit a large amount of heat when burned. However, they are only allowed to be used away from cities due to harmful emissions. Therefore, scientists are looking for ways to make the use of fuel oil more environmentally friendly.
When burned in a heating chamber, fuel oil is atomized by burners in the form of droplets - this is called primary grinding of the fuel. If the temperature and oxygen content in the chamber are not sufficient to ignite the fuel droplets, the volatile substances in them evaporate, causing the droplets to turn into solid particles that no longer burn. Such particles are involved in the secondary grinding of fuel: when colliding with them, fuel oil droplets are further “crushed”, which increases combustion efficiency. But if the drops are too large, they more often reach the walls of the boiler, contaminating them with soot. This leads to excessive heating of the walls and wears out the equipment. The smaller the droplets, the easier they ignite and the less soot they produce.
Employees of Tomsk Polytechnic University (Tomsk) studied how existing technologies can be changed to reduce the size of fuel oil droplets in boilers. Having recreated the boiler conditions in the sublimation chamber (lack of oxygen and high temperature), the researchers obtained solid particles from fuel oil droplets and studied their structure under a microscope. It turned out that the particles have a porous surface. At low impact speeds, the drop sticks to the porous particle, and the droplet grinding mode requires higher speeds. Next, at the experimental stand, the authors videotaped the collision of a drop with such a particle and analyzed the result. Scientists monitored how the grinding efficiency is affected by the size of the drop and particle, the angle of interaction between them, and the speed of the drop.
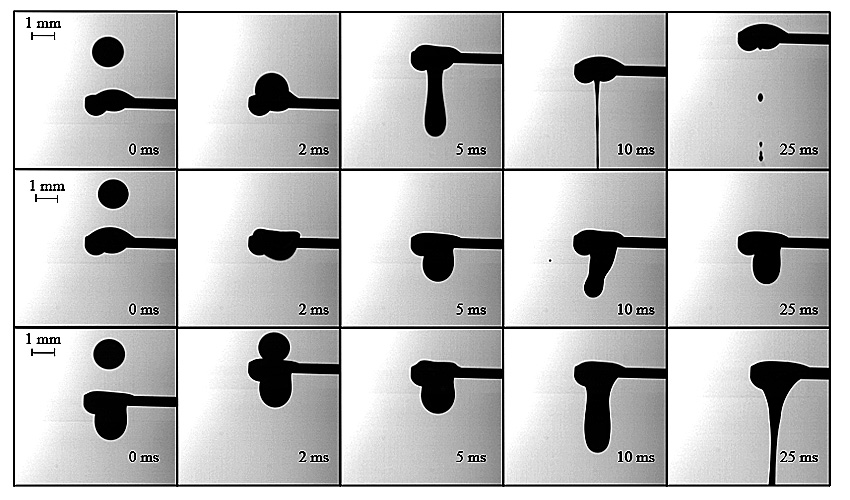
Video footage of the collision of water and fuel oil droplets with fuel oil particles
Based on these observations and previous research, the authors concluded that by positioning the burners that atomize fuel in a boiler or internal combustion engine at an angle of less than ten degrees to each other, production costs can be reduced by almost 10% due to more complete combustion of the fuel . In Russia, 2,357 boiler houses and seven thermal power plants operate on fuel oil; it is used on sea vessels. The modernization proposed by scientists will increase their efficiency. At the same time, the introduction of new technologies does not require large expenses and new equipment.“Such modernization of old equipment is easy to implement. This work is the first step to justify that it makes sense to move in this direction,” says Nikita Shlegel, Candidate of Technical Sciences, head of the project supported by the Russian Science Foundation, associate professor at the Research School of Physics of High-Energy Processes at TPU.Scientists emphasize that the use of water-fuel oil emulsion instead of pure fuel oil also increases the percentage of fuel burnout and reduces the level of hazardous waste. When the water content in the mixture is about 10%, the fuel drops undergo micro-explosions - the water heats up faster than the fuel oil and boils, splitting the drop into smaller parts.
“In the future, we plan to find other ways to improve the environmental friendliness of the use of fuel oil in order to expand the possibilities of its use. For example, by adding impurities that minimize emissions of harmful substances: soot and sulfur compounds,” added Nikita Shlegel.